Building a black wooden house requires careful planning and execution, whether you're building entirely new or refacing an existing structure. Focus on durable materials and meticulous craftsmanship.
Planning & Preparation
Design & Permits: Finalize architectural plans considering structure, drainage, and local building codes (setbacks, height restrictions). Secure necessary permits. Black surfaces absorb significant heat; factor in thermal expansion in design details.
Wood Selection: Choose decay-resistant species like Cedar, Redwood, Accoya, or pressure-treated lumber. Kiln-dried wood minimizes warping. For exterior cladding, vertical grain boards offer better stability.
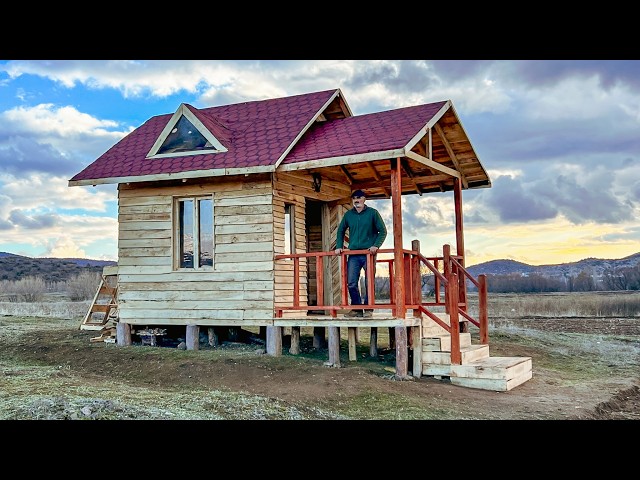
Black Finish: Select a high-quality, opaque black finish specifically formulated for wood. Options include:
- Opaque Stains: Penetrate wood while providing color (e.g., Cabot, Sikkens Cetol). Choose UV-resistant formulas.
- Paints: Provide a solid film layer (e.g., resilient acrylics or alkyds). Ensure excellent adhesion and flexibility.
- Charred Wood (Shou Sugi Ban): Traditional Japanese technique torching wood surface. Requires specialized expertise.
Construction Steps
Foundation:
- Beginners: Start with a simple, code-compliant foundation system like concrete piers or a perimeter beam. Ensure perfect leveling.
- Experts: Consider advanced foundation types (ICFs, frost-protected shallow foundations) requiring precise engineering.
Framing:
- Construct walls, floor(s), and roof using standard lumber framing techniques (platform framing common).
- Experts: Incorporate advanced framing for efficiency, complex roof designs, or pre-fabricated wall panels.
- Critical: Ensure robust structural bracing and waterproofing details at all openings and transitions.
Weather Barrier & Sheathing:
- Install exterior sheathing (OSB or plywood) over framing.
- Apply a high-performance water-resistive barrier (WRB) like housewrap or liquid-applied membrane. Seal all seams meticulously with specialized tape.
- Experts: Consider integrated WRB/drainage mat systems or rainscreen principles specifically behind dark cladding for enhanced moisture management.
Windows, Doors & Flashing:
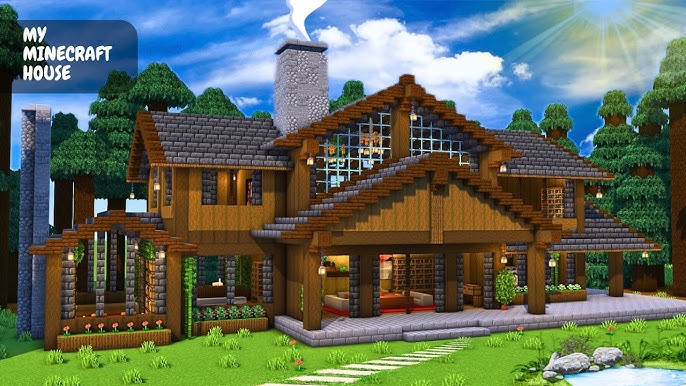
- Install high-quality, energy-efficient windows and exterior doors following manufacturer instructions.
- Integrate continuous flashing details meticulously at heads, sills, and jambs. This is paramount to prevent water intrusion behind dark cladding.
Exterior Cladding (Siding):
- Apply chosen wood siding (e.g., shiplap, board-and-batten, tongue-and-groove).
- Maintain consistent gaps (specified by manufacturer/finish) for expansion/contraction of black surfaces under heat.
- Prime all sides and edges of wood boards before installation (especially critical for end grains). Back-priming prevents moisture ingress from behind.
- Use corrosion-resistant fasteners compatible with the wood and finish (e.g., stainless steel or hot-dipped galvanized). Set slightly below the surface.
Finishing (The Crucial Step):
- Surface Prep: Sand to consistent smoothness (~80-120 grit). Remove all dust. Wood must be clean, dry, and weather-protected during application.
- Application: Apply the chosen opaque black stain or paint meticulously according to the manufacturer's specifications. Typically requires 2-3 coats for uniform coverage and maximum durability.
- Technique: Ensure complete, even coverage on all sides, edges, and ends of boards. Maintain a "wet edge" to prevent lap marks. Pay extra attention to joinery details.
- Environmental: Apply only within recommended temperature and humidity ranges. Avoid direct sunlight on drying surfaces.
Roofing & Trim:
- Install chosen roofing material.
- Add exterior trim pieces, ensuring tight joints and sealing. Paint/stain trim using the same high-quality products and techniques.
Maintenance (Critical for Black Wood)
Black wood shows dirt, fading, mildew, and imperfections easily. Expect significantly higher maintenance than lighter tones.
- Regular Cleaning: Wash annually or biannually with mild detergent and water to remove dirt and mildew.
- Inspection: Examine closely twice yearly for signs of finish breakdown, cracks, mildew, or water damage, especially at joints.
- Touch-ups: Address scratches, chips, or worn areas immediately to prevent moisture damage. Keep original finish for color matching.
- Recoating: Expect to fully refinish (clean, sand, reapply finish) every 3-7 years (depending on product quality, exposure, climate).
Key Considerations for All Builders
- Thermal Movement: Design and install cladding to accommodate significant expansion/contraction driven by solar heat gain on black surfaces.
- Moisture Management: Beyond WRB/flashing, ensure excellent site drainage (grade away from foundation), adequate roof overhangs, and proper ventilation behind cladding.
- Quality Over Speed: Meticulous installation, sealing, and finishing are non-negotiable for a durable, long-lasting black wooden house.