Choosing between DIY and buying a lean bench requires evaluating space efficiency and cost. Here's a targeted analysis:
Space Savings: DIY Often Wins
Customization: DIY allows precise tailoring to available space dimensions, minimizing wasted inches.
- Maximum Wall Fit: Build snugly against walls/obstacles where pre-built units often have fixed sizes.
- Profile Control: Reduce excessive depth; DIY can achieve
Pre-built Constraints: Standard sizes may not align perfectly with your layout, leaving inefficient gaps.
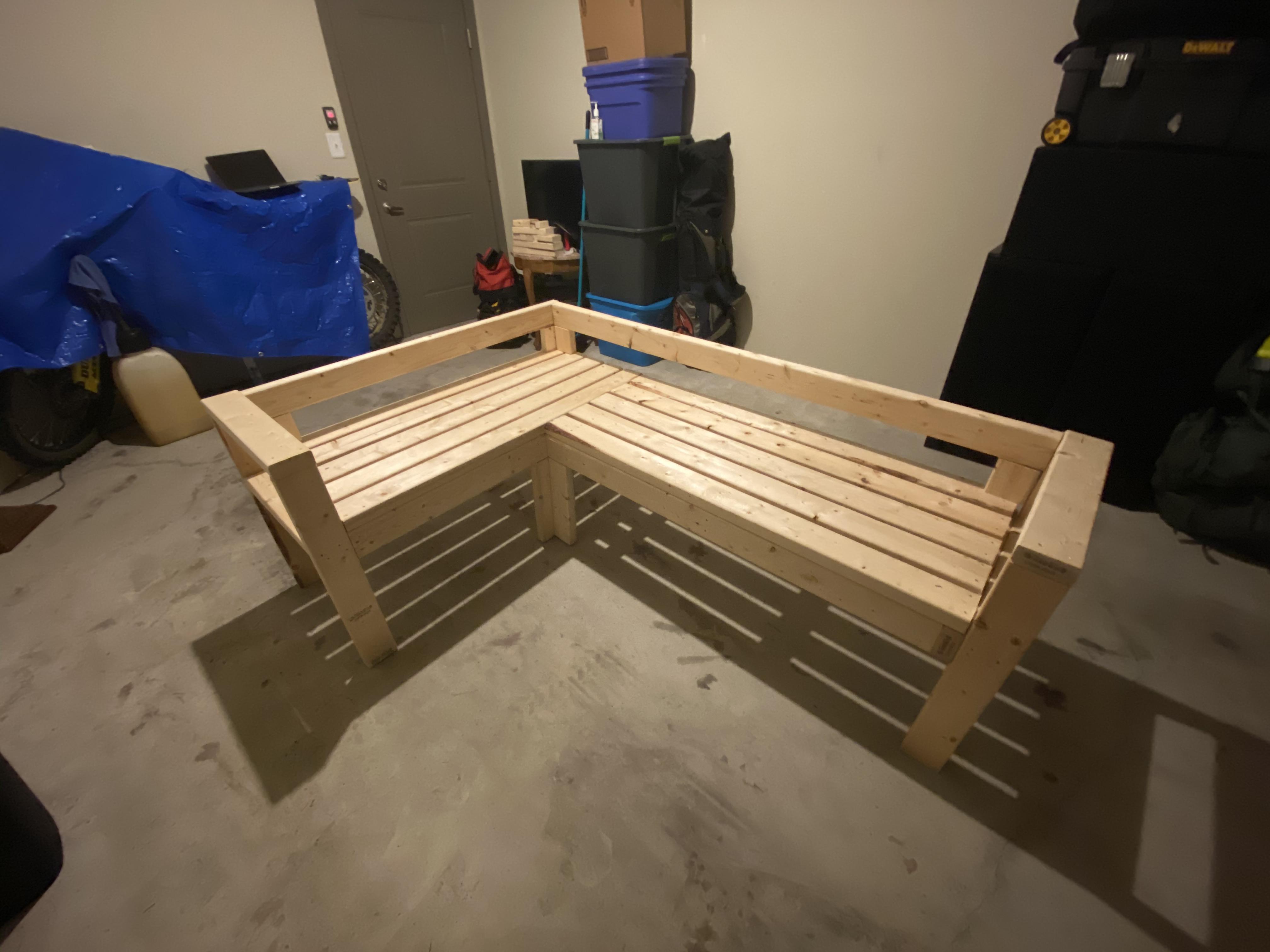
Cost Savings: Contextual
- DIY Cost Range: $50-$150 (materials only)
- Pre-built Cost Range: $100-$500+
DIY Wins When: Using basic materials like plywood/simple lumber, with tools already on hand. Saves 30-70% vs. equivalent quality.
Buying Wins When: Tools need purchasing or your labor value is high. Premium features (adjustable height, integrated clamping) cost more to DIY.
Critical Unspoken Factors
- DIY Time/Labor: Requires significant effort (design, build, finish). Factor in 8-15+ hours.
- Tool Access: Circular saw, kreg jig, clamps needed. Renting/buying impacts cost.
- Structural Integrity: Poor DIY designs risk failure. Pre-built units offer tested stability but may lack customization.
- Aesthetics: Commercial finishes often surpass DIY results without advanced skills.
Recommendation
- Prioritize Max Space Efficiency: DIY for bespoke sizing.
- Prioritize Lowest Cost & Quick Solution: Pre-built for basic models.
- Prioritize Premium Features/Finish: Buying usually makes sense.