Create custom 3D printed shoe soles by following this precise methodology. Disclaimer: Printed soles may lack the durability, flexibility, and safety standards of commercial footwear. Use at your own discretion, primarily for prototyping or low-impact situations.
Essential Materials & Tools
- Flexible TPU Filament: Minimum Shore 85A hardness (e.g., 95A) for basic functionality. Avoid rigid filaments like PLA.
- Calipers or Tracing Paper: For accurate foot measurement.
- CAD Software: Fusion 360, TinkerCAD, or dedicated footwear solutions (limited).
- Slicer Software: PrusaSlicer, Cura, etc.
- 3D Printer: Capable of TPU extrusion (direct drive strongly recommended).
- Adhesive: High-strength flexible glue (e.g., Shoe Goo, Barge Infinity).
Step 1: Capture Foot Dimensions
Trace both feet onto paper while standing. Measure:
- Length: Heel to longest toe (both feet).
- Width: Widest part across the ball.
- Arch Length: Heel to ball joint.
- Circumference: Ball and heel using a flexible tape measure.
Step 2: Design the Sole Geometry
Import foot outlines/images into CAD software. Build features considering:
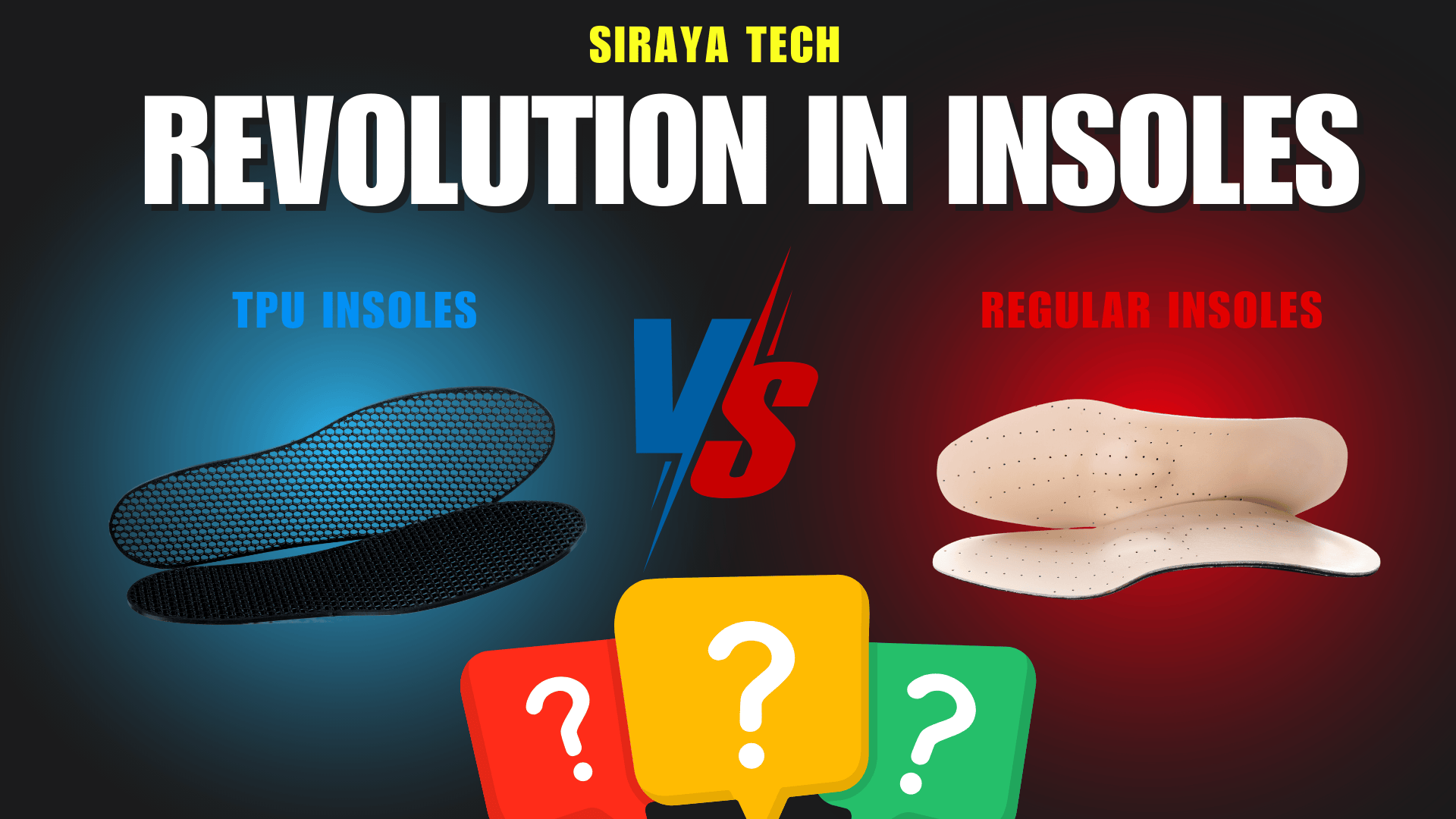
- Outsole Profile: 1-2mm larger than foot outline for stability.
- Thickness: Minimum 6-8mm core; thicker in heel/ball if needed.
- Midsole Geometry: Incorporate arch support contours based on measurements.
- Tread Pattern: Add shallow grooves for basic grip; sharp edges hinder flex.
- Stack Height: Heel > Forefoot for minimalist offset.
Step 3: Configure Slicer for TPU
- Infill: 50-80% gyroid or cubic pattern.
- Layer Height: 0.2-0.3mm for optimal layer adhesion.
- Walls: 3+ perimeters; increase for critical load zones.
- Print Speed: 20-40mm/s with retraction off or minimal.
- Flow Rate: Increase by 5-10% for dense material.
- Nozzle Temp: Consult filament specs (typically 220-235°C).
- Bed Temp: 40-60°C.
Use a brim or raft for adhesion.
Step 4: Post-Processing & Attachment
Remove supports carefully. Trim brim/raft. Apply adhesive to cleaned upper and cured sole surfaces. Secure firmly under pressure for 24-48 hours.
Critical Note: Rigorously test prototypes in safe environments. TPU may compress permanently or delaminate under load. This method suits experimental use only.